Digitization in mechanical engineering – an evolutionary process!
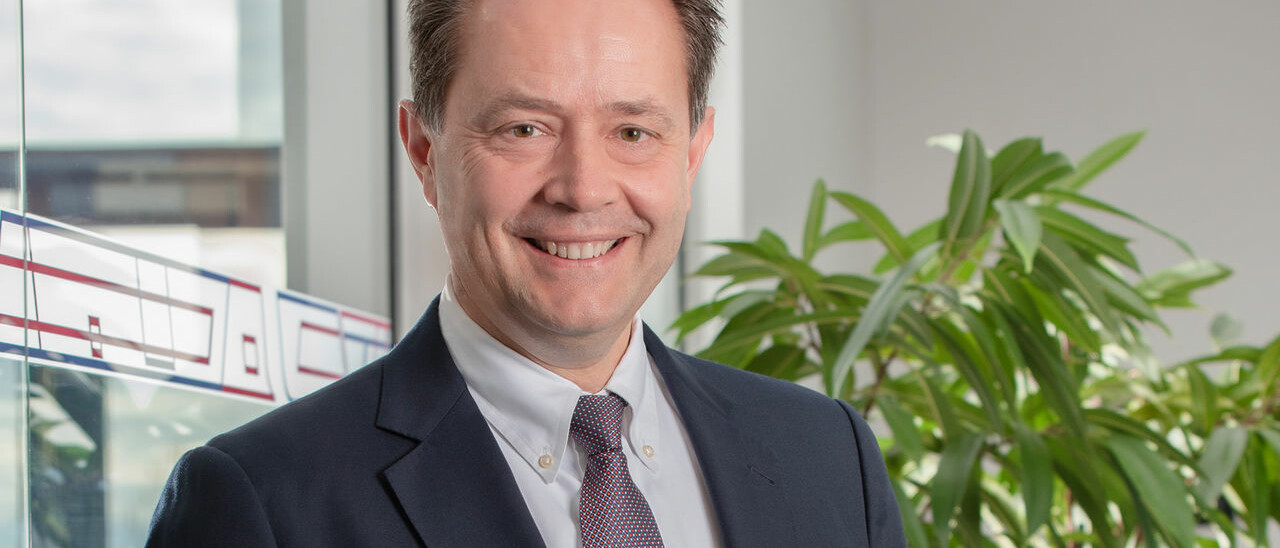
Current topics in the plastics processing industry include increasing energy efficiency in production, the circular economy, and the development and processing of non-petroleum-based polymers. Michael Wittmann, President of WITTMANN Technology in Vienna, emphasizes in an exclusive interview with P. E. Schall GmbH that personal exchange at the Fakuma 2021 attendance trade fair is unavoidable and an enrichment for getting to know the needs of customers and business partners.
What are the current and future challenges facing the plastics processing industry?
A very current challenge is the largely sluggish, sometimes inadequate supply of materials that preoccupies our industry and which was previously unknown in this form. However, according to popular opinion, this situation should ease again by the end of the year, early 2022. In addition, our customers and business partners are working very intensively on increasing energy efficiency in production and thus reducing CO2 emissions, the effects of a circular economy, and the development and processing of polymers that are not based on petroleum and offer the potential to be accepted by society in the long term. Likewise, increasing the level of digitalization and better production controls are important development trends in the companies.
How do you see German plastics processing companies positioned with regard to digitalization and automation?
The degree of digitization varies greatly depending on the size of the company. Likewise, there is a very different understanding of how the term “digitization” is interpreted depending on the contact person. Many small businesses (SMEs) with a machine park of up to around 25 SGMs understand digitization to mean the networking of internal business processes, in some cases also through integration into the supply chains of larger customers. For large companies, practically always with an international setup and an advanced degree of networking, digitization is moving in the direction of realizing a “glass factory”.
The digitization of machinery is progressing in Germany, but with a great deal of potential for the future. One stumbling block is the inadequate existence of standardized interfaces, since many peripheral devices are not yet covered by any Euromap standard and the standardization process is progressing relatively slowly. Another difficulty that applies to the machine industry in general is the very long service life of production machines. In some cases, older machines can only be digitized with a disproportionately large financial and technical outlay, which is then generally avoided. In this respect, digitization in the machine industry is a gradual process that is also taking place in this evolutionary form.
The industry is intensively engaged in the transformation from a linear to a circular economy. How far are we here?
Even today, injection molding machines are used for applications involving a wide variety of material grades. The material spectrum to be processed ranges from pure virgin material to regrind and regranulate to the processing of 100 percent regrind. The processing of recyclate in injection molding machines is not the great novelty or challenge, but rather a functioning collection system that ensures good separation and relatively high grade purity. A successful example of circular economy is the bottle-to-bottle recycling of PET bottles.
Plastics are ubiquitous in every area – and often do not have a good image. How do you think we can raise the profile of plastics?
As long as plastic waste is introduced into the environment in an uncontrolled manner, it will not be possible to raise the image of plastic. And as long as there are countries in the world that have not established a waste collection system, or one that does not function sufficiently, any kind of waste, and so also the long-lasting plastic products, will end up in the environment. This is not a causal problem of plastic, but stems from the fact that plastic is now found in so many applications in daily life and around the world. Any other material that is assigned little or no material value will meet the same fate. My assessment is thus that plastic will continue to live with a bad reputation, but will remain unavoidable due to its versatility and lower CO2 footprint compared to virtually all other materials. Biodegradable plastics would certainly be a solution, but they must first meet the numerous functionality criteria and not compete with the food industry.
How important is it for you personally or for your company to be present at trade shows and to exchange ideas with customers in person – specifically at Fakuma 2021?
A personal exchange is essential in our industry and an enrichment for getting to know the needs of our customers and business partners. In any case, we are looking forward to Fakuma 2021 and hope that it can take place in the communicated form in compliance with the currently given hygiene measures.
How have you been able to use the Fakuma-virtuell trade fair portal for yourself and your customers in recent months?
In our view, the trade show portal is particularly suitable for making information about exhibits shown at Fakuma easily accessible to interested parties for a longer period of time, or for arousing curiosity in the run-up to Fakuma and encouraging people to visit the trade show booth.
With which product highlight will you come to Fakuma 2021 in Friedrichshafen?
The highlight of our presentation this year from the injection molding machine sector is the new SmartPlus. This is a servo-hydraulic machine characterized by a high degree of economy, energy efficiency and stability. By using proven technologies and selected options, short delivery times and an excellent price/performance ratio can be offered for this machine in the future.
The robot series is being expanded to include the SONIC 108 high-speed unit – suitable for use on smaller injection molding machines with clamping forces of 50 tons and above. The revised WX153 robot will also be presented – the ideal automation solution for injection molding machines with 500 to 1,300 tons clamping force.
In the area of mold temperature control, two new devices will be presented. The TEMPRO basic Large 120 temperature control unit for use on large and heavy injection molds and the TEMPRO plus D200, the new water temperature control unit for high-temperature applications.
The successful series of CARD compressed air dryers also receives a double addition with the CARD primus 10S and the CARD primus 20S. In the case of CARD primus units, package solutions are offered that also include a conveying device with conveying hose and suction lance. CARD primus dryers are suitable for temperatures up to 200 degrees Celsius and have a wide range of applications.
In the recycling sector, WITTMANN is coming up with revisions of its G-Max 23 and G-Max 33 granulators. The units now have larger hopper openings, and the material outlet can now be selected between fixed and rotatable versions.