Industry Characterized by Change
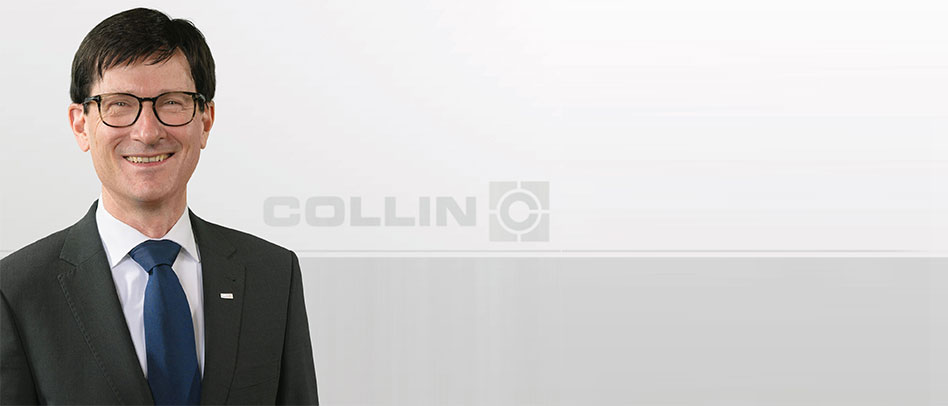
DI Dr. Friedrich Kastner, CEO / Managing Partner of COLLIN Lab & Pilot Solutions GmbH (image: COLLIN)
For COLLIN Lab & Pilot Solutions, Fakuma is one of the most important trade fairs in Europe, as confirmed by managing director Dr. Friedrich Kastner. He outlines current trends, topics and challenges in the plastics industry exclusively for trade fair promoters P. E. Schall. Amongst other things, this involves the continuous development of new, intelligent product structures and the adaptation of existing manufacturing processes.
Fakuma is one of the most important trade fairs for us in Europe, which is why we were on hand again in 2023 with three companies from the NGA Group. The clear-cut focus on the plastics industry is highly convincing and is also reflected by the large number of visitors at our booth, as well as the outstanding exhibitor mix.
Sustainability, E-mobility and Medical Technology are Driving Change
Demands placed on the plastics industry are extensive. Plastic products, along with their composition, optimisation and manufacturing processes, are changing rapidly and comprehensively. The main driving forces are sustainability, electromobility and medical technology. The challenges for R&D, companies in the plastics processing industry and machine manufacturers such as COLLIN are multifaceted. The goal is to increase the proportion of recycled material in the production of plastic products, optimise material composites, reduce film thicknesses and expand the functionalities of film layers. Demands for recyclability and the use of polymers in highly sensitive areas such as medical technology, aviation, the food industry, the automotive industry and battery production necessitate suitable solutions at all levels. Our mission is to continuously develop new, intelligent product structures, for example films with several layers including different, innovative layer functions. The next step is to test and improve these new film layer structures and make them reliable, stable and machine-compatible in preparation for production.
Polymer Processing Methods Need to be Adapted
As a consequence, processing methods for polymers have to be changed or adapted to new materials and their functions. For example, the introduction of metallocene polyolefins to multilayer extrusion, which are often difficult to process, poses new challenges for laboratory and production machines. The same challenge results when the proportion of recycled materials is increased. There’s also a trend towards foamed polyester multilayer products, which are stable, lightweight and easy to recycle because they consist of only one type of plastic despite having a multilayer structure.
Modern Energy Storage Systems Necessitate Improved Production Processes
Energy is also a current topic – in particular energy storage systems such as batteries and energy converters like fuel cells. COLLIN built the first electrode extrusion system more than 20 years ago. In the meantime, a large number of machines for battery development and production have been manufactured. The industry is challenged to continuously improve production methods and develop potentially alternative production processes which make more efficient use of resources and are more environmentally friendly. Lithium-ion batteries are currently the most promising answer to many energy storage issues. Efforts targeted at reutilisation and recycling need to take place downstream without delay.
Environmental and social requirements for plastic products necessitate appropriate product development as well as compliant laboratory, pilot and production facilities in order to access to market reliably in the end.